企业特色
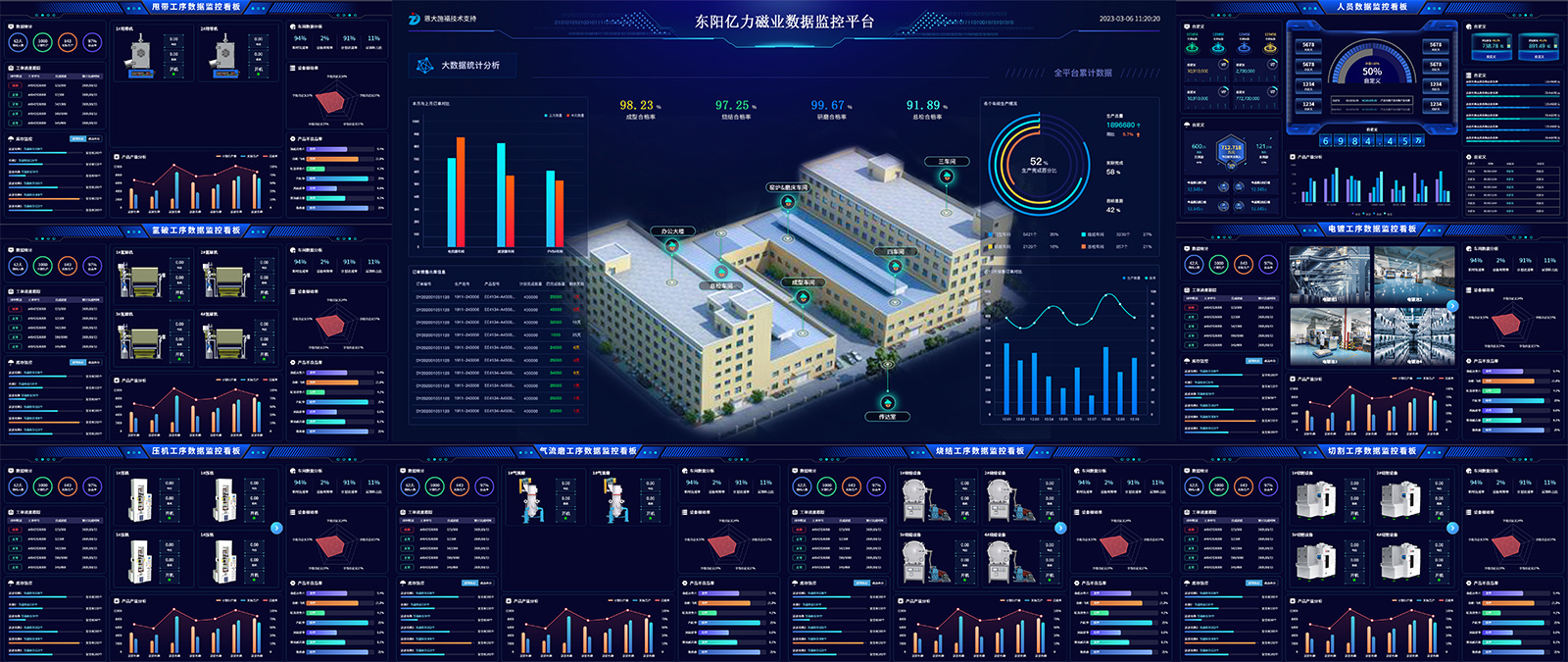
公司的主要产品为烧结钕铁硼永磁材料,生产模式为传统永磁材料行业生产模式,产品种类多、生产流程多、生产过程复杂。生产过程自动化程度低,生产效率不高,随着近些年国际环境复杂,企业利润下降,行业竞争激烈,公司必须通过由传统管理转型升级到数字化管理来降本增效、提质增效。通过引入生产管理软件建设数字化工厂实现经营层面从订单、生产、采购、仓库、财务;生产层面从生产计划管理、工艺管理、报工管理、出入库管理、品质管理、模具管理再结合设备物联、视觉识别等技术实现生产过程全面数字化、无纸化、透明化。
通过数字化工厂建设,解决当前企业生产、工艺、管理、制造及品控过程中的不足。对内实现研发设计、物料供应、生产制造、品质管理各环节的打通,对外实现供应链、产业链的数据共享。企业通过数字化工厂建设,依托大数据决策分析平台实现降本增效、提质增效的目的。
亿力磁业数字化工厂建设主要内容:
数字工厂建模
数字化建设的基础就是进行工厂模型数字化建设,通过系统基础资料的定义完成工厂人员、设备、工序、产品、BOM、工艺路线、工艺目标、工艺条件等数据的定义;通过对工艺设计的建立来数字模型,实现对产品工艺数字化定义与管理。
仓储物流管理
系统通过5G移动终端PDA条码识别并且与现有的ERP系统有效结合,记录并跟踪产品在企业内部物流中各个环节的情况,通过对库存产品的入库、出库、移动、盘点和拣货等操作进行全面的控制和管理, 实现智能化产品批次控制、快速出入库和动态盘点,通过自动识别算法有效的利用仓库存储空间,提高立体仓库的仓储能力。
核心设备智能化
各工序最新引入LYSC-600型真空甩带炉(甩带工序)、RVS–300KG晶界扩散炉(气流磨工序)、DX-1862/DX-1862R多线切割机(研磨工序)、BDES-350-250KN全电动磁场成型压机(成型工序)、XZHD-1200H旋转式真空烧结炉(烧结工序)等核心装备均带有自控制上位机系统和联网能力;实现数据实时读取、数据自动存储、异常信息自动推送、设备履历数据及时查询,设备运行过程数字化与透明化。
工厂物联网
通过对甩带炉、氢破炉,正空烧结炉、压机等设备进行改造,数字化平台系统根据设备运行情况,实时数据采集、报警和历史数据分析等。 同时设备保养计划的制定、编辑和审核,同时派发保养工单。故障管理包括设备故障报告录入、派发维修工单、逾期未排除故障提醒等;维修记录包括录入维修记录、查询维修记录功能,保养记录包括录入保养记录和查询保养记录功能。
品质数字化管控
系统结合当前物联网集成技术集成磁性行业常用到的量具(无线卡尺、无线千分尺、高度规、密度测试仪)等仪器,可实时进行测量数据的采集。数据采集到数据库后,系统通过数据中台,实现SPC品质控制,品质数据追溯,品质数据图形化分析。通过品质管理系统建立灵活、高效的制造过程控制体系,对制造过程的品质数据进行统计分析,加强实时监控,及时发现异常,快速处理,提高生产过程的稳定性,降低不良率,减少批量返工或报废的几率;建立产品追溯体系,实现对生产过程、物料和质量控制的快速追溯,并提高生产过程的纠错能力。
生产过程数字化
通过建设ERP、MES、SPC系统的订单管理、生产计划管理、工序扫描报工管理、现场统计、在制品管理实现产品从接单到生产的各关节通过系统实现生产环节数字化,系统可实时跟踪订单生产进度。生产过程中通过系统完成人、机、料、法、环、测有效协同,并且生产过程可以永久进行追溯。新增加SCM、CRM系统完善整个销售过程,实现全程可视化、高效协作,通过移动化应用更便捷、更高效的开展销售,提升现有生产性物资、非生产性物资的采购业务支撑和功能覆盖。
能源系统
通过加装或替换电表、水表、气体流量阀并结合物联技术实时采集电、水、气等磁性行业常用到的能耗。通过能源计划、监控、统计、分析、重点能耗设备管理和能源计量设备管理等多种手段,降低生产过程中单位产品能耗的信息化管控系统。
数据分析及可视化中控系统
通过建设数据中控室、车间可视化看板、移动APP系统应用实现对生产过程的实时数据和历史数据进行分析,对生产经营状况、市场需求、备品备件和设备维修计划等进行优化,实现智能化决策。通过车间看板实时反馈当前车间生产任务、设备生产状况、品质及异常,实现车间生产过程透明化、可视化。